As an expert in the electronics manufacturing industry, you have to have a deep understanding of PCBA related knowledge, which includes manufacturing, assembly, and prototypes. In this article, we will discuss PCBA prototype manufacturing. Whether you are in automotive, consumer electronics, aerospace or any other industry, these Both will be good for you.
Special PCBA Prototyping
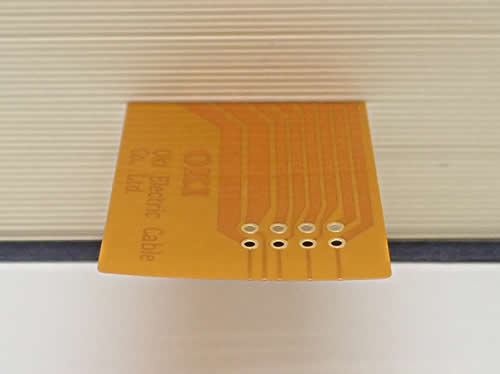
Compared to rigid PCB, FPCs are more challenging and costly to manufacture. Therefore, it is necessary to carry out prototype manufacturing to ensure that the board is functional before investing in the more expensive production process.
Flexible PCBA boards are composed of bendable film, copper foil, and adhesive, and they can withstand bending without damage when used in electronic products. These PCBAs are characterized by their thinness and high precision and have a multi-layer circuit structure, which makes them more difficult to produce. During PCBA prototype manufacturing, the processing plant attaches the chip to the circuit board or SMT components.
Like other substrates, electronics manufacturers are pursuing higher-level FPCBs with high voltage line density and a larger number of layers to improve PCBA performance, reduce electronic products’ size, and transmission power consumption. However, the FPCBA manufacturing process is complex, and the processing factory needs to put in more effort into prototype manufacturing. Moreover, electronic components’ application on FPC requires more attention.
Flexible PCBA (FPCBA) can be found in various electronic fields. It is an indispensable component in any high-tech product. Communication products such as smartphones use FPCB extensively. Additionally, FPCB is used in notebook computers, automotive electronics, medical, military, wearable devices, among others. As modern products become lighter, thinner, and shorter, flexible PCB importance has grown. For example, statistics show that about 20 FPCs are used in an iPhone X. FPCs also serve as antenna FPCs, backlight module FPCs, camera lens FPCs, touch screen soft boards, Touch ID soft boards, sim card soft boards, laptop screens, connecting flexible boards, automotive image sensor flexible boards, and car light unit flexible boards, illustrating the importance of flexible boards.
FS Technology uses PI, MPI, and LCP to manufacture flexible PCBA prototypes, depending on the material characteristics. MPI is Modified PI, as PIs have mostly been eliminated due to poor performance. Currently, the materials used in flexible boards are mainly MPI and LCP, with LCP offering higher performance but at a higher cost. In terms of cost-effectiveness, MPI has always been considered relatively high, with its performance improving significantly in recent years and even posing a threat to LCP. In 2018, Apple decided to replace the LCP soft board with the MPI soft board to cut expenses. The primary consideration in using these three types of flexible boards is operational attenuation. The loss of 3 does not make much difference when the frequency is low. However, as the frequency increases, PI’s loss gradually increases, and the loss of MPI and LCP also has a significant difference. Therefore, LCP’s advantage is more evident at higher frequencies. With the 5G era, some transmission frequencies will significantly increase to above 24GHz, and there will be higher quality requirements for soft boards.
Surface treatment during PCBA prototype manufacturing
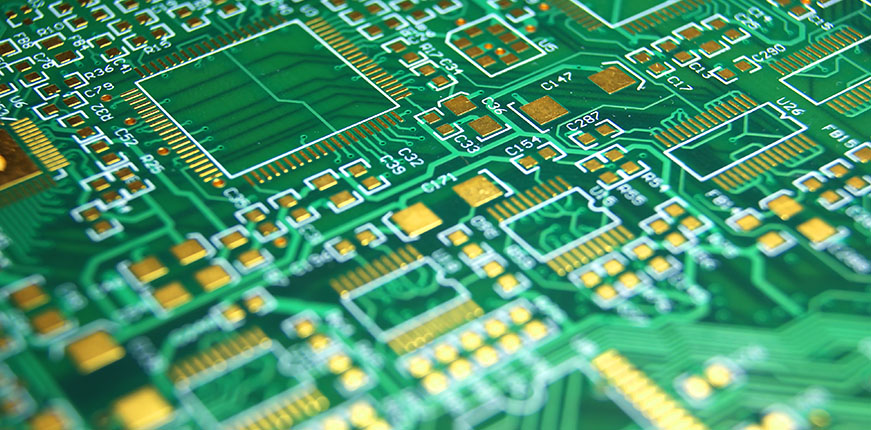
To ensure the performance and durability of a PCBA Prototyping, surface treatment is an essential step. The surface treatment helps to protect the copper surface of the PCBA from environmental factors such as humidity, oxidation, and corrosion, which can degrade the board’s performance and shorten its lifespan. The treatment also prepares the board for subsequent processes, such as soldering and component placement.
The most basic and cost-effective PCB surface treatment is the bare copper board, which is simply a board with a copper surface that has not undergone any surface treatment. This method is usually used for low-cost prototypes or in applications where the board will not be exposed to harsh environmental conditions.
The Hot Air Solder Leveling (HASL) surface treatment involves dipping the board in a molten tin-lead alloy and then leveling it with hot air. This method provides good solderability, but it has become less popular in recent years due to environmental concerns and the trend towards lead-free alternatives.
Lead-free HASL is similar to HASL but uses lead-free alloys, making it more environmentally friendly. However, this method can be more expensive than traditional HASL.
Chemical gold plating is a common surface treatment method that provides excellent protection against corrosion and oxidation. This method involves immersing the board in a gold plating solution, which deposits a thin layer of gold onto the copper surface. Gold plating is ideal for applications that require high reliability and performance, such as aerospace or military applications.
Gold plating is a more expensive surface treatment method that provides the highest level of protection against oxidation and corrosion. This method involves depositing a thicker layer of gold onto the copper surface, making it ideal for applications that require repeated use and handling.
Chemical silver is another surface treatment method that provides excellent protection against oxidation and corrosion. This method involves depositing a thin layer of silver onto the copper surface using a chemical process. Chemical silver is often used for low-cost applications where performance and reliability are not critical.
Organic Solderability Preservatives (OSP) board is a surface treatment method that uses a thin layer of organic material to protect the copper surface from oxidation and corrosion. OSP provides a flat and uniform surface that is ideal for fine pitch components, and it is often used in high-speed applications such as telecommunications or data transmission.
Key points to understand for PCBA prototyping

Courier service provider: Fast turnaround is essential for courier services, and FS Technology collaborates with renowned courier companies like DHL, Fedex, UPS, TNT, and EMS. Additionally, we have our own forwarder that offers lower shipping costs.
Means of transportation: Multinational trading companies can provide express, air, rail, and sea transportation based on the customer’s preferences and budget.
Popular areas: PCBA prototype manufacturing services are applicable to various industries, ensuring product quality in sectors such as semiconductors, smart homes, medical products, smart wearables, industrial control, and the Internet of Things.
Prototype manufacturing discount: Offering free prototypes is usually a misleading claim found online. However, discounts are available for high-volume products.
Choosing a prototyping company: Many prototyping companies exist in China, such as FS Technology, JCP, PCBway, among others.
Quality Control: Quality control is crucial in PCBA prototyping, and all products undergo testing before shipping to ensure they are in perfect condition.
Quotation: Typically, the quotation time for prototyping is shorter than for mass production.